Asbestos inspections are vital for protecting your health and safety. You might not know that these inspections can identify hidden asbestos sources, preventing severe conditions like lung cancer and mesothelioma. During an inspection, certified professionals assess the materials in your environment, documenting their condition and potential risks. Inspections are mandatory before renovation or demolition to comply with health regulations. Regular checks furthermore help manage asbestos-containing materials effectively. Knowing the status of asbestos can influence real estate decisions and budgeting. Understanding these inspections better can substantially impact your safety measures and decision-making.
Importance of Asbestos Inspections
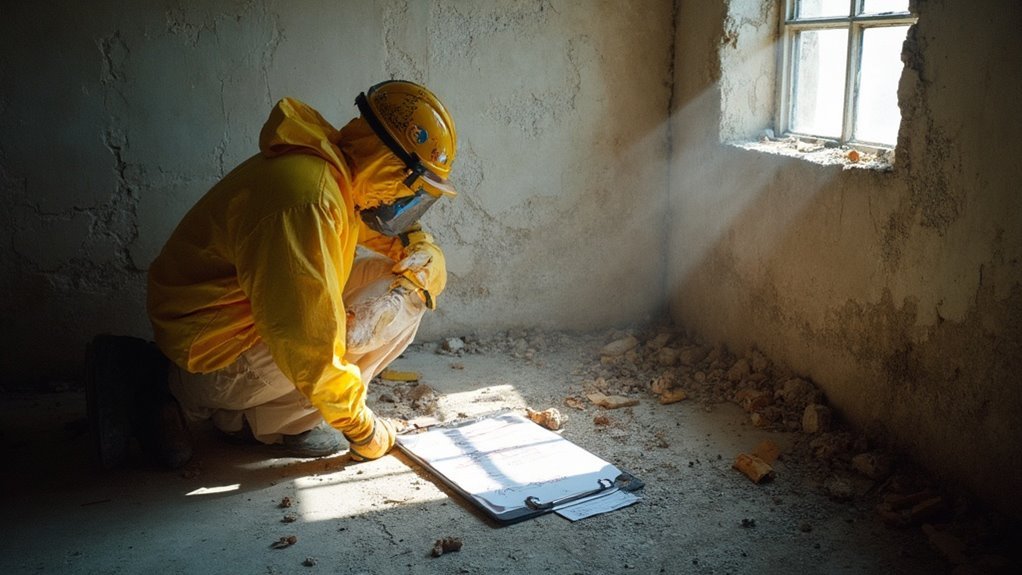
The importance of asbestos inspections cannot be overstated, as they play a critical role in safeguarding public health. Many people fall prey to asbestos myths, believing that older buildings aren't a concern or that visible damage is the only risk. In reality, asbestos fibers are microscopic and can be easily inhaled, leading to severe health issues like lung cancer, mesothelioma, and asbestosis. Furthermore, asbestos exposure is often linked to various cancers, which underscores the need for vigilance.
Understanding the inspection significance is crucial for your safety and that of your family. Regular inspections help detect potential sources of asbestos contamination early, allowing for prompt remediation actions. This proactive approach not only minimizes health risks but also guarantees a safer environment for everyone. Additionally, conducting a thorough asbestos survey is essential before any renovation or demolition to ensure compliance with legal and regulatory requirements.
Furthermore, legal and regulatory requirements mandate asbestos surveys before renovation or demolition. Failure to comply can result in significant liabilities and health risks. For homeowners and buyers, knowing the status of asbestos can inform real estate decisions, budgeting, and future renovations. By addressing asbestos concerns through professional inspections, you're taking fundamental steps to protect yourself, your family, and your investment from the hidden dangers lurking in your environment.
The Inspection Process
During the inspection process, you'll start with an initial assessment to identify and document suspect materials. This includes collecting bulk samples for laboratory analysis to confirm the presence of asbestos. Finally, you'll need to report your findings accurately, ensuring compliance with regulatory requirements. Additionally, the inspection process must include the identification of ACMs to effectively manage potential health risks.
Initial Assessment Steps
As you begin the initial assessment steps for an asbestos inspection, a thorough approach is essential to guarantee safety and compliance. This process consists of two main components: a historical review and a visual inspection.
- Historical Review: Start by identifying potential asbestos-containing materials (ACMs) based on the building's age and construction.
- Interviews: Conduct interviews with building occupants and owners to gather insights into the building's history and potential asbestos exposure.
- Record Review: Examine maintenance, renovation, and repair records to pinpoint areas where asbestos might be present.
- Blueprint Analysis: Review building maps and blueprints to locate suspected ACMs.
Next, perform a detailed visual inspection. A certified asbestos inspector will look for materials likely containing asbestos, such as insulation, flooring, and ceiling tiles. The inspector assesses the condition of these materials to determine the risk of asbestos fiber release, noting their location and accessibility.
This thorough initial assessment not just helps in identifying probable ACMs but likewise sets the stage for further action, ensuring that safety protocols are adhered to from the very beginning.
Sampling and Analysis
Sampling and analysis are significant components of the asbestos inspection process, guaranteeing accurate identification and assessment of potential risks. Proper sample collection and analytical methods are critical for reliable results.
Stage | Description | Purpose |
---|---|---|
Sample Collection | Samples are collected in airtight containers. | Prevents asbestos escape. |
Analytical Methods | Stereomicroscopy, PLM, and TEM are used for analysis. | Identify and confirm asbestos type. |
Safety Procedures | Work is conducted under negative pressure with HEPA filters. | Protects analyst and environment. |
During the inspection, samples are opened under controlled conditions to avoid contamination. Analysts employ stereomicroscopy for initial fiber identification, progressing to Polarized Light Microscopy (PLM) for confirmation. For smaller concentrations, Transmission Electron Microscopy (TEM) is crucial.
It's important to understand the limitations of each method. While PLM can confirm the presence of asbestos, it doesn't quantify it, and point counting is necessary for accurate assessments. By adhering to regulations and employing these analytical methods, you can guarantee a thorough and compliant asbestos inspection, protecting both health and safety.
Reporting Findings Properly
Properly reporting findings from an asbestos inspection is fundamental for guaranteeing safety and compliance. Accurate documentation not only protects occupants but likewise meets legal obligations. Here's what you need to include in your report:
- Location: Identify where each material containing asbestos is found.
- Condition: Describe the status of each material, especially if it's damaged.
- Inspector Details: Sign the report and include your certification number and date.
- Certification: Attach a photocopy of your current asbestos inspector certificate.
Adhering to documentation standards is critical. After the inspection, you may need to follow up with Operations and Maintenance, repair, encapsulation, enclosure, or removal, depending on the findings. Remember, building owners are responsible for guaranteeing that certified inspectors conduct surveys and that reports comply with local regulations.
Maintaining records according to regulatory requirements is significant; they may need to be kept for specific durations as dictated by the EPA and local labor departments. Prioritize reporting accuracy to safeguard health and guarantee compliance with the law.
When Inspections Are Required
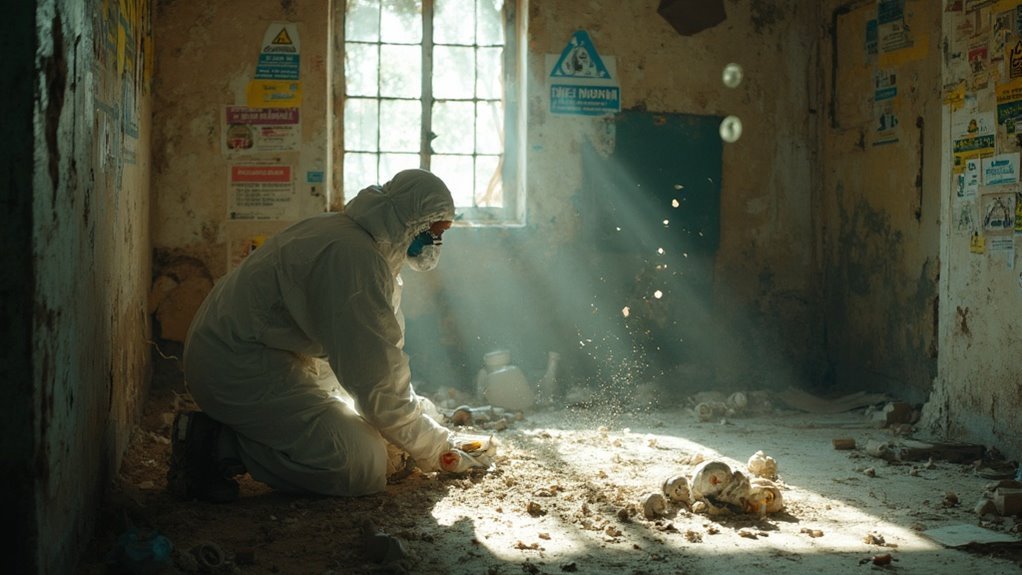
A thorough understanding of when asbestos inspections are required is crucial for building owners and contractors. Compliance with asbestos regulations is critical, especially before renovation or demolition activities. Here's a quick overview of when inspections are mandated:
Situation | Inspection Requirement |
---|---|
Public Buildings | Asbestos surveys required before renovation (TAHPR, NESHAP) |
Commercial Facilities | Inspections by a Cal/OSHA Certified Asbestos Consultant (CAC) regardless of age (SCAQMD Rule 1403) |
Educational Institutions | Mandatory inspections and management plans under AHERA |
Renovation or Demolition | Notify DSHS at least 10 working days prior to disturbing RACM or ACBM |
Annual Inspections | Required for non-residential properties, particularly schools |
Inspection timelines vary based on the specific project and regulatory framework. Always verify inspections are conducted by certified professionals without conflicts of interest. Following these requirements helps prevent hazardous exposure to asbestos and guarantees compliance with local and federal regulations. Understanding when inspections are necessary can safeguard your project and the health of those involved.
Types of Asbestos Inspections
Asbestos inspections can be categorized into several types, each serving a distinct purpose based on the context of the building's use or planned activities. Understanding these types helps guarantee safety and compliance:
- Management Surveys: These are conducted during normal occupancy to identify asbestos-containing materials (ACMs) within accessible areas. Sampling confirms the presence of asbestos, allowing for ongoing building use and maintenance.
- Refurbishment Surveys: Before any renovation work, these surveys identify ACMs that could be disturbed. They are targeted and intrusive, opening hidden surfaces to guarantee safe practices.
- Demolition Surveys: Conducted before demolition, these surveys identify all ACMs requiring safe removal. They involve intrusive inspections of hidden areas and must be performed with the building vacated.
- Reinspection Surveys: Regular inspections of known or presumed ACMs verify they remain in good condition. The frequency varies based on risk, with thorough reviews every five years.
Common Inspection Challenges
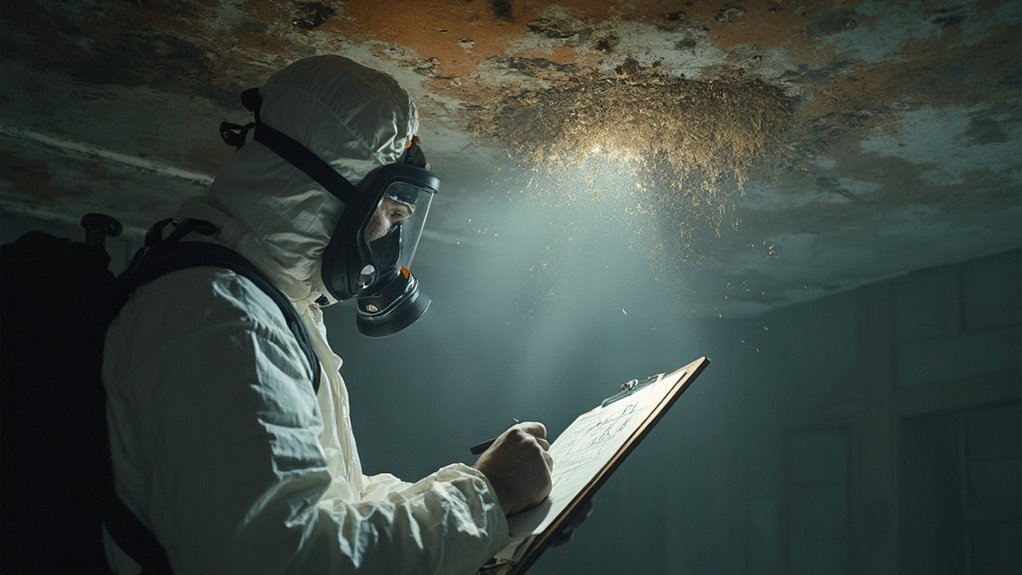
Maneuvering the complexities of asbestos inspections can present numerous challenges that impact the effectiveness of the process. One major hurdle is access barriers—locked doors and restricted areas can prevent surveyors from thoroughly examining all spaces. Property owners or occupants may be uncooperative, which can lead to incomplete surveys and missed potential risks.
Additionally, structural diversity in buildings complicates the detection of asbestos-containing materials (ACMs). Varied architectural styles and construction methods necessitate specialized techniques for accurate identification. For instance, historical buildings often conceal hidden ACMs, making detailed surveys crucial.
Sampling and analysis further compound these challenges. To guarantee accurate identification of ACMs, representative sampling is critical; nonetheless, inadequate sampling can result in false negatives. The absence of standardized sampling protocols adds to this issue, as does the need for specialized equipment.
Finally, regulatory and compliance challenges emerge, as traversing different jurisdictional regulations can be complex. Staff turnover in regulatory agencies may hinder enforcement, creating inconsistencies. These factors underscore why overcoming these common inspection challenges is significant for effective asbestos management.
Benefits of Professional Inspections
Professional asbestos inspections provide vital risk mitigation strategies by accurately identifying and evaluating materials that may contain asbestos. This precise evaluation helps you manage potential hazards effectively and guarantees compliance with health regulations. By staying informed about the condition of your property, you considerably reduce health risks and improve overall safety for occupants.
Risk Mitigation Strategies
When it comes to safeguarding your property and health, engaging in professional inspections for asbestos detection is critical. These inspections not only guarantee compliance but also play a key role in risk mitigation. Here are four key benefits you should consider:
- Hazard Identification: Certified inspectors perform thorough examinations, identifying potential asbestos-containing materials (ACMs) that may pose risks.
- Risk Evaluation: Professionals conduct extensive risk assessments, evaluating the condition of ACMs and the likelihood of exposure, allowing you to make educated choices.
- Preventive Measures: By detecting asbestos early, you can prevent harm to residents and workers, considerably reducing the risk of exposure and related diseases.
- Enhanced Property Value: Demonstrating that your property has been professionally inspected and is free from asbestos can increase its market value.
Engaging expert inspectors guarantees proper handling and containment of samples, reducing the likelihood of fiber release. Their detailed reports outline the type, extent, and risk level of any ACMs found, providing you with peace of mind and a clearer understanding of your property's safety. Prioritizing professional inspections is imperative for effective risk management.
Accurate Material Assessment
Engaging in accurate material assessment is vital for effectively managing asbestos risks in your property. This process involves employing various material evaluation methods to identify asbestos-containing materials (ACMs) that may be present. Certified inspectors utilize visual assessments and detailed physical examinations to spot potential ACMs, while sampling and laboratory analysis confirm the presence and type of asbestos fibers.
The use of scoring algorithms, such as those developed by the Health and Safety Executive (HSE), plays an important role in evaluating the condition of these materials. Each parameter—product type, damage extent, surface treatment, and asbestos type—is scored to calculate an overall Material Assessment Score. This score helps prioritize which ACMs require immediate attention, ensuring that you address the most hazardous materials first.
Regulatory Compliance and Liability
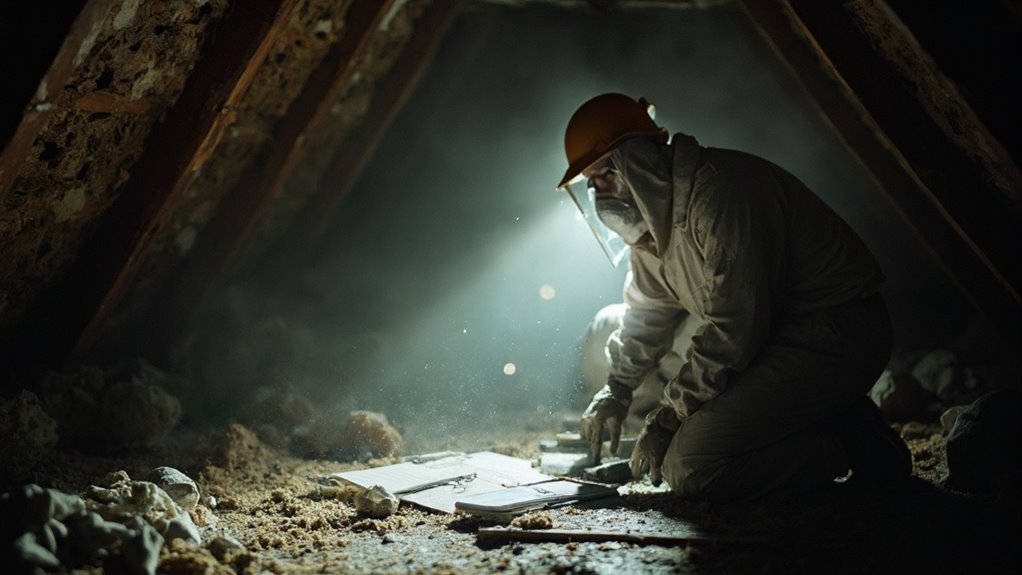
Navigating through the intricate terrain of asbestos regulations is vital for guaranteeing compliance and minimizing liability risks. Understanding the regulatory frameworks and their implications can protect your organization from legal repercussions. Here are four key compliance requirements you should consider:
- Conduct Asbestos Surveys: Before any renovation or demolition, verify a certified asbestos inspection is performed to identify potential ACMs.
- Notify Authorities: Always submit notifications to state or local air program authorities prior to starting any work that may disturb asbestos.
- Follow Abatement Protocols: Retain licensed asbestos abatement contractors and adhere to local regulations for handling and disposing of asbestos materials.
- Document Everything: Maintain thorough records of inspections, assessments, and compliance efforts to demonstrate due diligence.
Failure to comply with these regulations can lead to significant liability implications, including hefty fines and potential legal action. Regular inspections and adherence to guidelines not only protect public health but additionally shield you from costly penalties. By understanding and following these regulatory requirements, you can mitigate risks and contribute to a safer environment.
Health Risks of Asbestos Exposure
Understanding the regulatory environment surrounding asbestos not only protects your organization from legal ramifications but also emphasizes the severe health risks associated with asbestos exposure. Asbestos diseases such as asbestosis, lung cancer, and mesothelioma can develop after prolonged exposure, often with a latency period of 20 to 50 years.
Here's a concise overview of the health risks associated with asbestos:
Asbestos Disease | Description |
---|---|
Asbestosis | Scar tissue in lungs, causing breathing issues. |
Mesothelioma | Cancer affecting lung and abdominal membranes. |
Lung Cancer | Increased risk, particularly in smokers exposed to asbestos. |
Pleural Disorders | Includes pleural plaques, thickening, and effusions. |
Non-malignant Issues | Conditions like pleural thickening, often because of occupational exposure. |
Your risk stems from various exposure routes, including occupational settings, environmental proximity to asbestos mines, and secondary exposure through family members. Importantly, there's no safe level of asbestos; any exposure can lead to serious health consequences. Recognizing these risks is essential for effective prevention and public health initiatives.
Frequently Asked Questions
How Long Does an Asbestos Inspection Typically Take?
An asbestos inspection typically takes at least one day, but inspection duration varies based on factors like building size, age, and complexity. Expect longer times for refurbishment or demolition surveys and when access is limited.
Can Homeowners Perform Asbestos Inspections Themselves?
While you might be tempted to take the DIY route, the risks involved are like playing with fire. Professional inspections are a necessity, ensuring accurate results and minimizing hazards from asbestos exposure. Don't gamble with safety.
What Should I Do if Asbestos Is Found?
If you find asbestos, implement immediate containment measures, follow safety protocols, and hire professional abatement. Guarantee compliance with disposal regulations, manage materials properly, and address potential health risks and legal obligations throughout the process.
How Often Should Asbestos Inspections Be Conducted?
Think of asbestos inspections like a lighthouse guiding you through fog. You should conduct them every six to twelve months for regulatory compliance and risk assessment, ensuring safety from hidden dangers in your environment.
Are There Specific Certifications Required for Inspectors?
Yes, there are specific certifications required for inspectors. You'll need to meet certification prerequisites, complete accredited training requirements, and pass examinations to guarantee you're knowledgeable about asbestos properties and safety protocols.