Your home might not be safe from asbestos, a toxic substance linked to serious health issues like lung cancer and mesothelioma. Asbestos can be found in older buildings, and without proper inspections every 6-12 months, you may overlook its presence. Expert abatement services are crucial for identifying and safely managing asbestos-containing materials. Certified professionals utilize effective techniques, like encapsulation and removal, ensuring compliance with safety regulations. By engaging experts, you reduce health risks and secure a safer living environment. There's more to understand about maintaining long-term safety and the importance of proper procedures in managing asbestos-related concerns.
Understanding Asbestos Risks
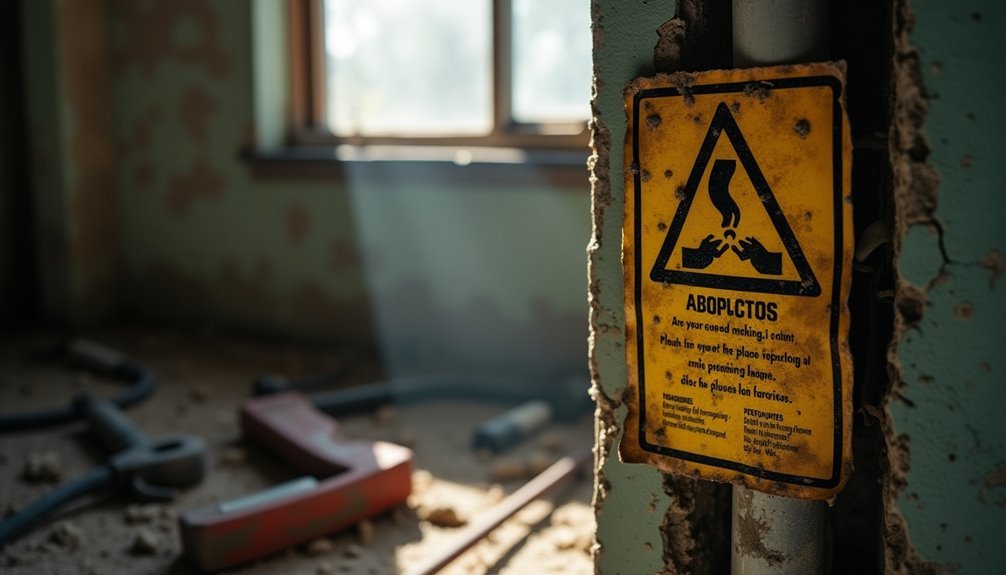
Understanding the risks associated with asbestos exposure is crucial for protecting your health and safety. Asbestos exposure can lead to severe health implications, including lung cancer, mesothelioma, and various nonmalignant lung disorders. Even minimal exposure can result in mesothelioma, a rare but often fatal cancer that affects the membranes surrounding your lungs or abdominal cavity.
Moreover, asbestosis—a debilitating lung disease caused by asbestos fibers—can develop over time, leading to a buildup of scar-like tissue that impairs your lungs' ability to supply oxygen to your body. If you smoke and are exposed to asbestos, your risk of lung cancer increases significantly compared to nonsmokers with the same exposure levels.
It's essential to recognize that no amount of asbestos is considered safe; even small quantities can pose serious health threats. Furthermore, the long-term effects of asbestos exposure may take decades to manifest, often resulting in irreversible damage. With around 2,500 to 3,000 new mesothelioma cases diagnosed each year in the U.S., understanding these risks isn't just about awareness—it's about taking proactive steps for your health and well-being. Approximately 3,000 cases of mesothelioma are diagnosed annually in the U.S., highlighting the urgent need for awareness and preventive measures.
Importance of Inspections
Conducting regular inspections for asbestos is vital to ensure the safety of both workers and occupants. Federal and state regulations mandate these inspections to protect against the risks associated with asbestos exposure. You should schedule inspections before any renovation, demolition, or abatement activities to assess potential hazards effectively. Typical inspection frequency is every 6-12 months to monitor known asbestos-containing materials (ACMs) and to identify any new ones.
Inspection techniques include visual examinations conducted by certified inspectors, along with sampling and laboratory analysis to confirm the presence of asbestos. This thorough approach helps in developing an asbestos register and management plan based on your specific findings. Regular updates to this register ensure ongoing compliance with legal requirements, such as the Control of Asbestos Regulations 2012. Furthermore, risk mitigation through these inspections can significantly reduce the likelihood of airborne asbestos fibers during construction activities.
Neglecting inspections can expose you to serious health risks and legal repercussions, including fines for non-compliance. Moreover, failing to identify ACMs can lead to unexpected costs and project delays. By prioritizing inspections, you create a safer environment and demonstrate due diligence in managing asbestos risks effectively.
Identifying Asbestos Materials
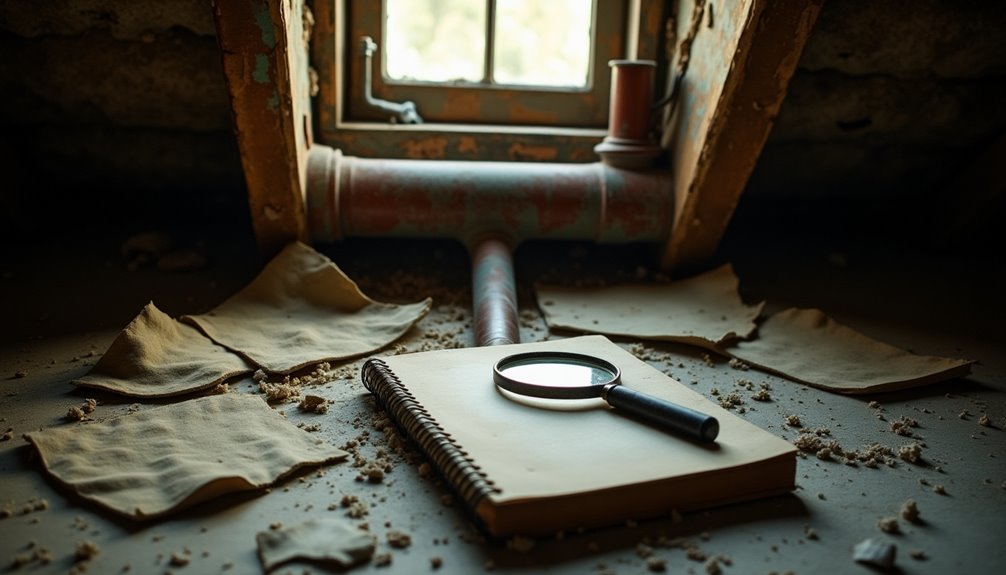
How can you effectively identify asbestos materials in your environment? Start by understanding the common types and products that contain asbestos. Asbestos testing is crucial since many materials may appear harmless but can be hazardous when damaged. Here's a quick reference table to help you with material identification:
Material Type | Common Appearance | Asbestos Presence |
---|---|---|
Building Materials | Ceiling tiles, shingles | High in older constructions |
Automotive Products | Brake linings, clutch plates | Used for insulation |
Insulation Products | Pipe lagging, sprayed insulation | Found in thermal systems |
As you inspect your home, look for these materials, especially in ceilings, walls, and floors built before the 1980s. Remember, individual asbestos fibres are microscopic and only visible under a microscope—so don't rely on visual cues alone. If you suspect the presence of asbestos, it's best to seek professional asbestos testing. Identifying these materials is the first step in ensuring a safer living environment. Your health depends on it!
When to Consider Abatement
You should consider abatement when you notice signs of damage to asbestos-containing materials (ACM), such as cracks or crumbling. Conducting a thorough risk assessment is crucial to determine the potential hazards associated with damaged ACM. Always seek a professional inspection to ensure accurate evaluation and safe handling of any asbestos issues.
Signs of Asbestos Damage
Recognizing the signs of asbestos damage is crucial for maintaining a safe home environment, especially in houses built between the 1940s and 1970s. With approximately 70% of structures from this era still containing asbestos-containing materials (ACMs), vigilance is key. Look for these indicators of potential damage:
Signs of Damage | Description | Health Implications |
---|---|---|
Visible Cracks or Breaks | Damaged ACMs can release fibers. | Increased risk of respiratory diseases. |
Water Damage | Moisture can deteriorate asbestos. | Potential for airborne asbestos fibers. |
Exposed Insulation | Disturbed insulation is highly risky. | Direct exposure to harmful fibers. |
Deteriorating Flooring | Vinyl or linoleum may show wear. | Risk of inhaling released fibers. |
Aging Ceiling Tiles/Roofs | Damage indicates potential release. | Long-term health risks from exposure. |
If you observe any of these signs, it's vital to consider professional asbestos detection and abatement services. Disturbing ACMs can lead to significant health implications, including asbestosis and cancer. Don't take chances—act swiftly to protect your home and health.
Risk Assessment Importance
After identifying signs of asbestos damage, it's important to assess the associated risks to determine the need for abatement. Conducting a thorough risk assessment helps you identify potential health hazards related to asbestos exposure, which can lead to severe illnesses such as lung cancer and mesothelioma. Given the long latency periods of these diseases, the urgency for assessment cannot be overstated.
Legal compliance is also a crucial factor; many countries mandate risk assessments before any work that might disturb asbestos-containing materials (ACMs). Non-compliance can result in significant fines and legal ramifications. By understanding the risks, you can formulate effective control measures—such as encapsulation or removal—that prioritize the safety of building occupants and workers.
Planning and preparation are vital in this process. A comprehensive risk assessment outlines the scope of work, expected exposure levels, and necessary permits, ensuring a smooth abatement process. By identifying high-risk areas, you can allocate resources wisely and implement specific procedures for monitoring and maintaining ACMs. Ultimately, a proactive approach protects not just your property, but also the health and safety of everyone involved.
Professional Inspection Necessity
When planning renovations or demolitions, the necessity for a professional asbestos inspection becomes critical. You must ensure that any asbestos-containing materials (ACMs) are identified and managed to prevent health risks. This is especially true if your property was built before 1980, as many older buildings contain hidden hazards.
Key Considerations | Details |
---|---|
Inspection Frequency | Recommended before any major renovations |
Inspector Qualifications | Must be certified and trained in asbestos management |
Hiring a qualified inspector is essential to safely identify ACMs. They will perform thorough examinations and utilize laboratory analysis to detect hidden dangers within walls or flooring. By adhering to local regulations, you not only protect your health but also avoid legal liabilities associated with improper handling of asbestos.
Abatement Techniques Explained
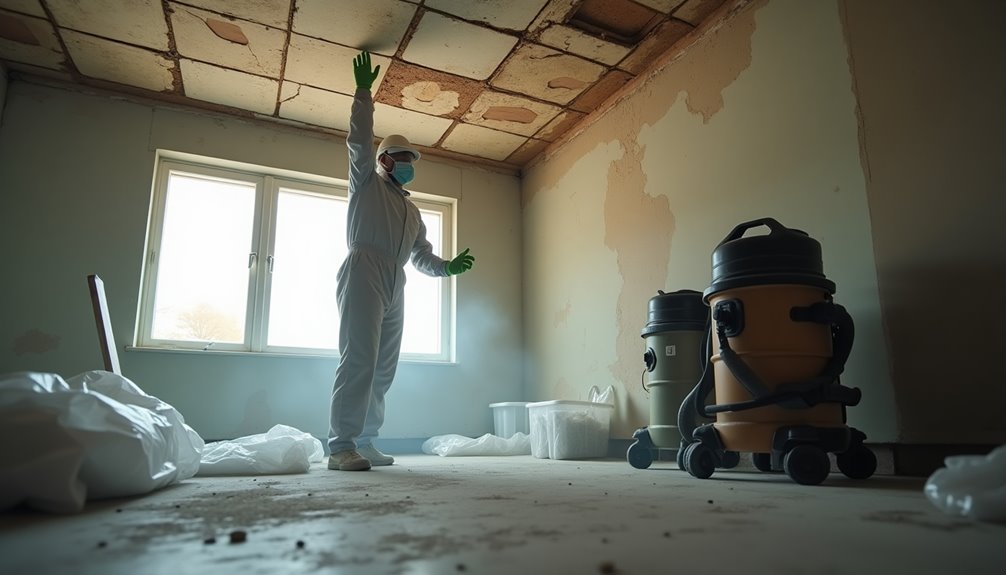
When addressing asbestos concerns, you can choose between two primary abatement techniques: encapsulation and removal. The encapsulation method involves sealing materials to prevent fiber release, while the removal process entails completely eliminating asbestos-containing materials from your property. Understanding the steps and applications of each technique is crucial for ensuring safety and compliance during abatement.
Encapsulation Method Overview
Encapsulation serves as a vital technique in managing asbestos-containing materials (ACMs), allowing you to effectively mitigate health risks associated with exposure. This method involves applying a specialized coating that binds asbestos fibers, preventing them from becoming airborne. Here are three key encapsulation benefits:
- Cost-Effectiveness: Encapsulation typically costs less than removal, reducing labor and disposal expenses.
- Minimal Disruption: Unlike removal, encapsulation causes little disturbance, making it ideal for situations where removal may be impractical.
- Reduced Health Risks: This technique significantly lowers the chances of asbestos fibers releasing into the air, thus minimizing health risks.
The encapsulation process includes thorough assessment and survey of ACMs, ensuring the right encapsulant is selected for compatibility with the material. Surface cleaning and risk evaluation are critical steps before applying the encapsulant using various techniques, such as sprays or rigid boards. After application, the encapsulant undergoes curing, followed by testing to confirm that it effectively contains asbestos fibers. By opting for encapsulation, you're choosing a strategic, long-term solution for managing ACMs while ensuring safety in your environment.
Removal Process Steps
Successfully removing asbestos-containing materials (ACMs) requires a meticulous approach that prioritizes safety and compliance with regulatory standards. The removal process begins with a thorough inspection and assessment by certified inspectors. They identify and confirm the presence of ACMs through visual examinations and laboratory testing.
Next, a detailed abatement plan is developed. This plan outlines the scope of work, containment measures, and safety protocols. You must notify regulatory agencies and obtain necessary permits before proceeding. The work area is then cleared of personal belongings and sealed off using plastic sheeting and negative air pressure machines.
During the removal process, specialized tools and wet methods are employed to minimize dust generation. Wetting the ACMs helps reduce fiber release, while HEPA filter vacuums and wet cleanup tools prevent airborne particles. It's crucial that workers wear protective clothing and respirators throughout this phase.
Cleaning and clearance follow the removal. HEPA vacuums thoroughly clean the work area, and air quality testing ensures safety standards are met. Finally, asbestos waste is disposed of in licensed landfills, adhering strictly to asbestos regulations to maintain a safe environment for you and your family.
Benefits of Professional Services
Although handling asbestos removal on your own might seem tempting, the benefits of hiring professional services far outweigh any perceived advantages. By opting for expert abatement, you ensure compliance, reduce health risks, and minimize disruption in your space. Here are three key benefits:
- Ensuring Compliance: Professionals adhere to local, state, and federal regulations, obtaining necessary permits and following legal requirements for safe asbestos removal and disposal.
- Reducing Health Risks: Licensed experts significantly lower the exposure risk to harmful asbestos fibers, improving air quality and protecting both occupants and workers from serious health conditions.
- Minimizing Disruption: Skilled contractors execute the abatement process efficiently, ensuring minimal interruption to your daily activities. Their experience allows for a streamlined approach, from inspection to cleanup.
In terms of cost benefits and service comparisons, investing in professional services ultimately saves you time and money by preventing future asbestos-related issues. With the right professionals, you gain peace of mind, knowing your environment is safe and compliant, all while protecting your property investment.
Preparing for Abatement
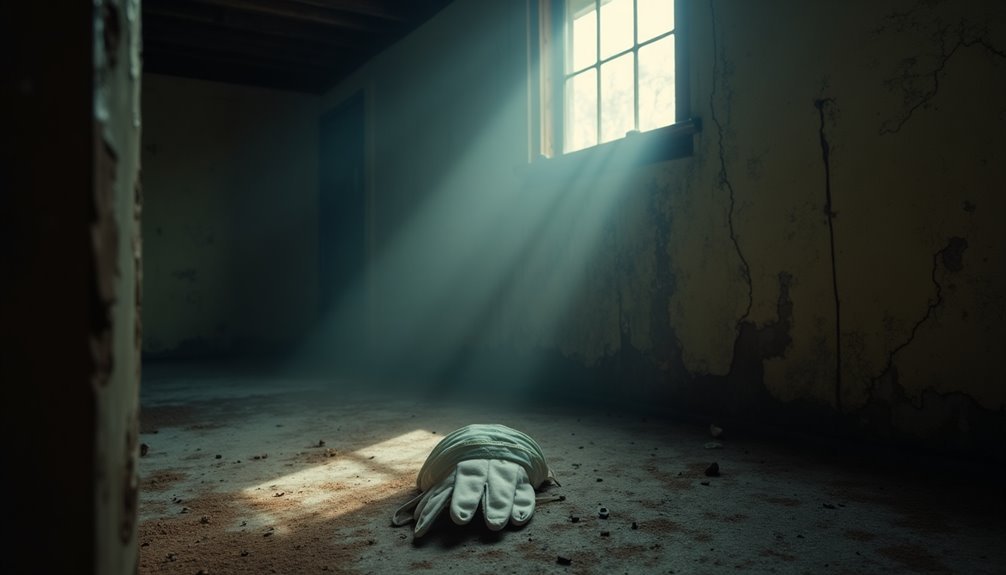
Before beginning the abatement process, it's crucial to prepare the area properly to ensure safety and compliance. Start by conducting a thorough inspection to confirm asbestos presence. Develop a detailed abatement plan that outlines the scope of work, abatement timeline, safety measures, and legal compliance. Notify appropriate regulatory agencies and obtain necessary permits before any work begins.
Set up an enclosure using plastic sheeting to seal all windows, doors, and ventilation ducts, creating a controlled environment. For smaller areas, a mini-enclosure may be appropriate. Implement negative-pressure systems to prevent air leakage and establish airlocks for safe entry and exit of workers, as well as for the removal of bagged waste. Accredited air monitors should conduct inspections to verify the adequacy of the enclosure.
Worker training is essential to ensure that all personnel are equipped with the knowledge they need to handle asbestos safely. Provide personal protective equipment (PPE), including disposable coveralls, head covers, and foot covers, to prevent fiber contamination. By adhering to these preparatory steps, you can significantly mitigate risks associated with asbestos abatement.
Execution of Abatement Process
To effectively execute the abatement process, you need to prioritize thorough preparation and planning. Implementing strict safety measures is crucial to protect both workers and occupants during the operation. Finally, post-abatement verification ensures that all asbestos has been safely removed and the environment is free from harmful fibers.
Preparation and Planning
Effective preparation and planning are crucial for a successful asbestos abatement process. You need a well-structured approach to ensure safety and compliance with regulations. Here are three key steps to focus on:
- Development of an Abatement Plan: Create a detailed outline that identifies the scope of work, containment measures, and worker safety protocols. Tailor this plan to your project, considering the best removal, encapsulation, or enclosure methods while ensuring regulatory compliance.
- Inspection and Assessment: Conduct a thorough property inspection to identify asbestos-containing materials (ACMs). This includes visual examinations and laboratory testing to confirm the presence and condition of ACMs.
- Notification and Permitting: Notify the appropriate regulatory agencies before starting the abatement process. Obtain all necessary permits to ensure adherence to local and federal regulations. It's essential that all stakeholders are informed about the project timelines and the abatement procedure.
Safety Measures Implemented
Safety measures implemented during the execution of the asbestos abatement process are vital for protecting both workers and building occupants. Adhering to strict safety protocols and containment strategies minimizes exposure to hazardous asbestos fibers.
Phase | Safety Measures |
---|---|
Site Demarcation | Sealed work area with plastic sheeting and duct tape |
Material Removal | Use of PPE and specialized tools, including HEPA vacuums |
Containment | Negative air pressure systems with HEPA filters in place |
Cleanup and Decontamination | HEPA vacuuming and thorough decontamination procedures |
The work area is isolated to ensure that no occupants enter, effectively preventing the spread of asbestos fibers. During material removal, asbestos-containing materials (ACMs) are either removed or encapsulated using specialized equipment. Containment ensures that fresh air is drawn into the work area while filtered air is expelled, further safeguarding everyone involved. After all materials are removed, thorough cleanup and decontamination follow to eliminate any remaining fibers. These measures not only protect workers but also ensure that building occupants remain safe throughout the abatement process.
Post-Abatement Verification
Post-abatement verification is crucial for ensuring the environment is safe after asbestos removal. This process involves several key post abatement procedures to confirm that all asbestos has been effectively managed. Here are the essential steps you can expect:
- Visual Inspections: A final visual inspection is conducted to check for any dust or remaining asbestos-containing materials (ACM). Inspectors focus on hard surfaces and difficult-to-reach areas to ensure thoroughness.
- Airborne Sampling: Certified professionals collect air samples both indoors and outdoors using high-efficiency particulate air (HEPA) filtration. This minimizes fiber dispersal and adheres to federal guidelines.
- Laboratory Analysis: Samples undergo analysis using transmission electron microscopy (TEM), the EPA's preferred method. This analysis determines if airborne asbestos levels comply with legal standards.
Completion of these steps ensures that the area is safe for re-entry and that all necessary clearance testing has been performed by an unbiased team. Remember, proper verification not only protects your health but also grants peace of mind, allowing you to enjoy your space without fear of asbestos exposure.
Post-Abatement Safety Measures
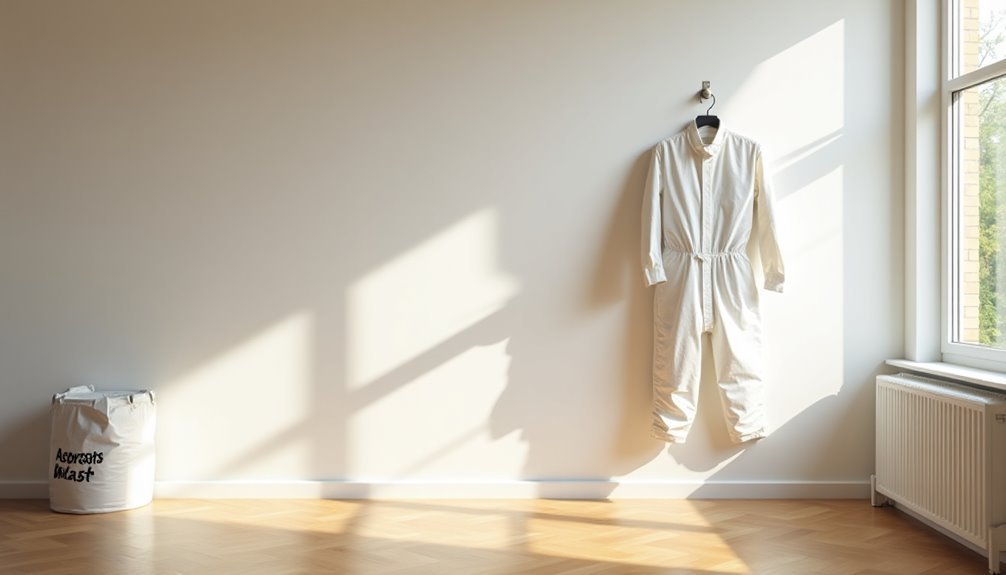
After an asbestos abatement project, ensuring the area is safe for reoccupation is crucial. Conduct thorough air quality testing to confirm that no airborne asbestos fibers remain. It's vital to use certified professionals for these post-abatement inspections, as they ensure compliance with EPA and OSHA regulations. Obtain certification that the abatement was successful and the area meets public health standards.
Proper disposal of asbestos materials is also essential. Place all asbestos waste in leak-tight, clearly marked containers, double-bagging to prevent fiber escape. Transport these materials to approved disposal sites while keeping detailed records of the process for compliance verification.
In addition, prioritize worker and equipment decontamination. Workers should shower and wash their hair immediately after completing the abatement. Decontaminate tools and equipment using wet rags and HEPA-filtered vacuum cleaners, adhering to strict disposal protocols for personal protective equipment.
Finally, inform neighbors of the work to maintain public safety. Close all windows and doors, and keep household members, visitors, and pets away from the work area until it's cleaned and declared safe. Taking these proactive post-abatement safety measures will help ensure a secure environment.
Long-Term Asbestos Management
Long-term asbestos management is essential to ensure the ongoing safety of building occupants and the integrity of the structure. Implementing an effective asbestos lifecycle management plan can help minimize risks associated with asbestos-containing materials (ACM). Here are three key components to focus on:
- Inspection and Assessment: Regularly conduct thorough inspections with certified professionals to identify and assess the condition of ACM. Early detection of wear and tear is crucial to prevent fiber release.
- Operations and Maintenance (O&M) Programs: Develop a comprehensive O&M program that includes training, cleaning protocols, and maintenance practices. This minimizes exposure to asbestos fibers and ensures ACM remain in good condition.
- Regulatory Compliance: Stay informed about local, state, and federal regulations. Ensure all abatement efforts are conducted by accredited professionals, and obtain necessary permits to maintain compliance.
Incorporating sustainable abatement solutions into your long-term asbestos management strategy not only protects occupants but also contributes to environmental health. By addressing these areas, you can achieve a safer living or working environment while preserving the integrity of your property.
Conclusion
In conclusion, ensuring your home is safe from asbestos isn't just about compliance—it's about protecting your loved ones from hidden dangers. By investing in expert abatement services, you're not just removing a risk; you're reclaiming peace of mind. Think of your home as a fortress; safeguarding it from asbestos is crucial to keeping your castle secure. Stay proactive with inspections and management to ensure a healthy environment for years to come. Your family's future depends on it.