Asbestos inspections are essential for protecting your health in spaces with potential asbestos-containing materials. You'll begin with an initial assessment that involves reviewing construction records and conducting interviews. A thorough visual inspection will look for signs of damage, followed by sampling of suspect materials like insulation or walls. These samples are analyzed in certified labs to identify asbestos presence accurately. After the inspection, you'll receive a comprehensive report detailing findings and recommended actions. Understanding this process not only helps you feel secure but ensures compliance with regulations, revealing why these inspections are vital to your safety. More insights await you ahead.
Importance of Asbestos Inspections
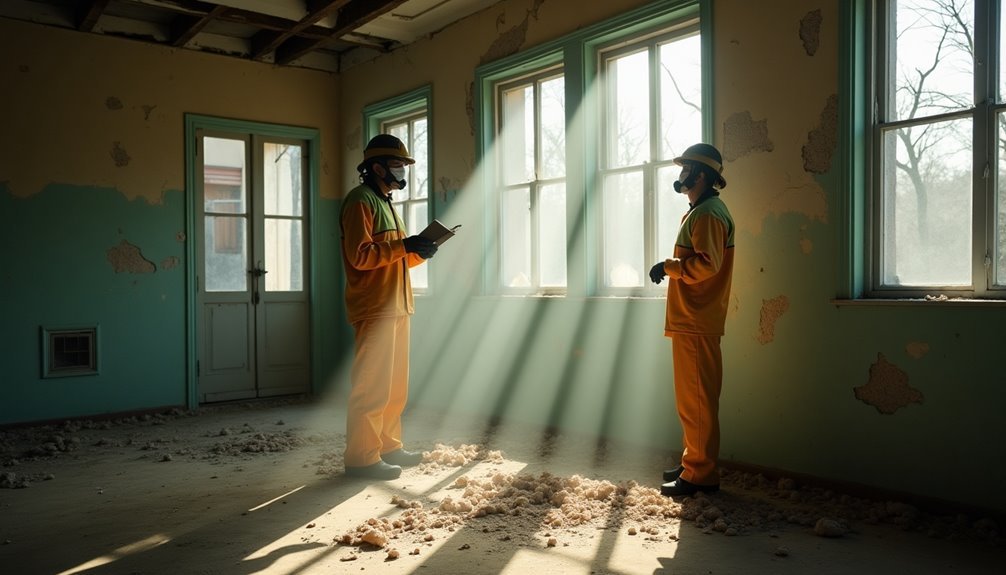
Asbestos inspections are vital for ensuring health and safety, especially in environments where asbestos-containing materials (ACMs) may be present. Identifying ACMs is crucial, as these materials can release harmful fibers when disturbed, posing significant health risks. Inhalation of asbestos fibers can lead to severe conditions like lung cancer, mesothelioma, and asbestosis. Regular inspections minimize exposure risks and foster a healthier environment for everyone involved. Regular inspections also benefit homeowners by identifying minor issues early, contributing to transparency and fairness in real estate processes.
Compliance with asbestos regulations is essential to avoid legal ramifications. Federal mandates, such as those from OSHA and the US EPA, require thorough inspections, particularly before renovation or demolition. For instance, in California, only certified consultants can conduct asbestos surveys, ensuring adherence to legal standards and protecting you from costly fines and project delays.
Initial Assessment Process
The initial assessment process for identifying asbestos-containing materials (ACMs) involves a systematic approach that combines historical research, interviews, and accessible area inspections. It begins with a thorough historical review of the building, where you'll explore construction records, plans, and past renovations to pinpoint periods when asbestos was commonly used. This sets a foundation for understanding potential ACMs present in your building.
Next, you'll conduct interviews with current and former occupants, maintenance personnel, and construction workers. These conversations help gather crucial information about known asbestos materials, their current condition, and any previous incidents related to asbestos exposure.
Following this, an accessible area inspection takes place, where you visually assess areas like walls, ceilings, and floors for signs of ACMs. You'll look for physical damage or degradation that may indicate the presence of asbestos. It is important to note that the inhalation of fibers can lead to significant health risks associated with asbestos exposure.
Finally, based on the collected data, you'll establish a detailed inspection plan. This plan outlines the scope, areas to inspect, and necessary inspection techniques, ensuring a methodical approach to further assessments and risk evaluations. This initial assessment is essential in safeguarding health and ensuring compliance with safety regulations.
Detailed Inspection and Sampling
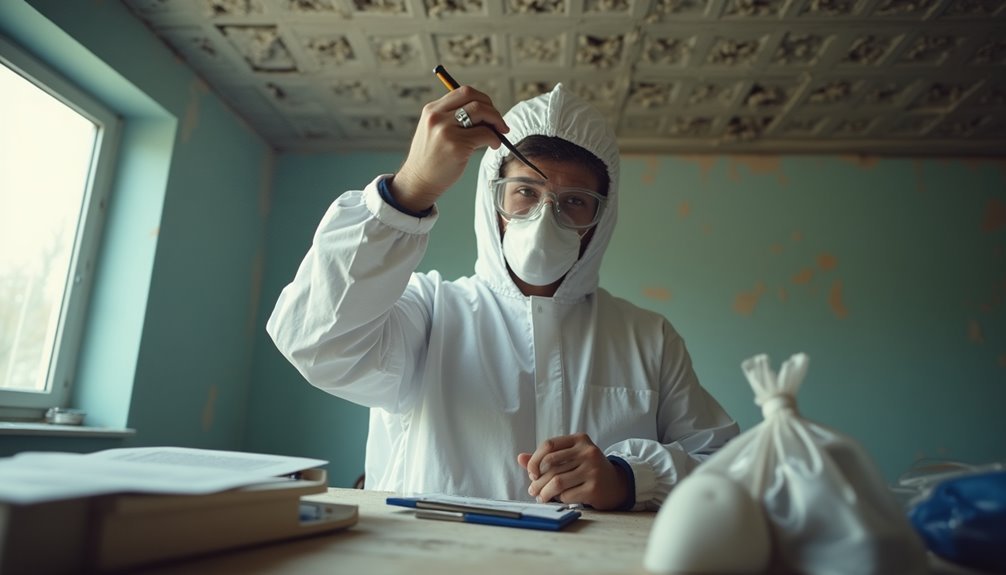
A thorough detailed inspection and sampling process is crucial for accurately identifying asbestos-containing materials (ACMs) within a property. During this phase, you'll conduct a detailed assessment that begins with a visual inspection, looking for signs of deterioration such as tearing or abrasions. You'll also evaluate whether materials are friable or non-friable, documenting your findings for future reference.
Next, you'll inventory suspect materials, identifying items like concrete flooring, walls, and pipe insulation. Sampling techniques will involve collecting bulk samples from these materials, adhering to specific regulations on the number of samples taken. It's important to sample from multiple locations to ensure an accurate representation of the materials present.
The sampling strategy might employ methods like the "chocolate chip cookie theory," where you focus on the manufacturing process to guide your sampling approach. This detailed inspection and sampling are vital for determining the presence of ACMs, thus guiding future actions and ensuring safety. By engaging in this meticulous process, you empower yourself and others to make informed decisions regarding asbestos management.
Analyzing Laboratory Results
Upon completing the detailed inspection and sampling, it's time to analyze the laboratory results to confirm the presence and concentration of asbestos. Samples are sent to a certified lab where advanced laboratory techniques like Polarized Light Microscopy (PLM) and Transmission Electron Microscopy (TEM) are employed. These methods not only detect asbestos but also quantify it, ensuring you understand the risk involved.
Initial observations focus on the sample's appearance and physical characteristics, while preparation techniques involve suspending residues in fiber-free water and filtering them onto a membrane. PLM typically detects asbestos concentrations of less than 0.1%, with TEM handling lower concentrations. The laboratory counts fibers using a 1000-point count method to provide aerial estimates of asbestos types, such as chrysotile and amosite.
Result interpretation is crucial; a positive result confirms asbestos presence, detailing fiber types and concentrations. Reports are structured to display findings clearly, often including photographs and mapping of asbestos locations. If no asbestos is detected, the report states "No asbestos detected in sample" (NADIS). Understanding these results empowers you to make informed decisions regarding safety and remediation.
Post-Inspection Actions and Reporting
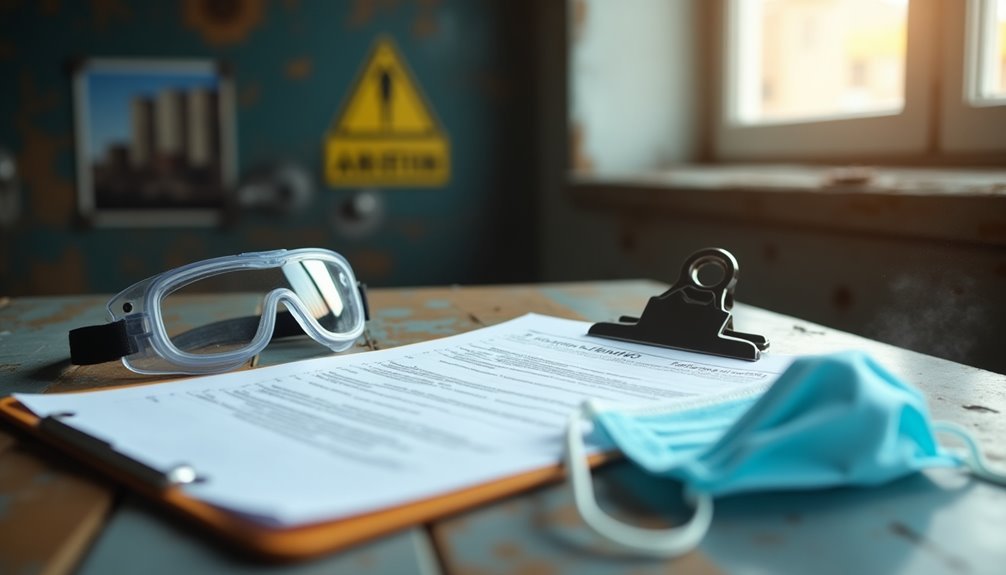
After completing the asbestos inspection, it's essential to follow through with comprehensive reporting and assessment actions. Your Asbestos Survey Report must clearly identify all suspect materials and those confirmed to contain asbestos. This report includes a separate results table summarizing materials that tested positive, detailing their description, location, quantities, condition, and percent asbestos content.
Key components of the report include the sampling method, lab qualifications, and analytical procedures to ensure compliance with regulatory requirements. Attaching the sample chain of custody, laboratory analysis results, and diagrams of sampling locations is crucial for transparency and verification. Remember, the report needs to be certified by a Cal/OSHA Certified Asbestos Consultant (CAC) with a wet signature.
Post-abatement verification is crucial as it involves visual inspections to confirm the work area is clean and free from residue. These inspections don't replace air monitoring but ensure that the area meets standards for reopening. Your report should outline any necessary remedial actions based on the site contamination assessment, ensuring compliance with both local and federal regulations. By adhering to these protocols, you ensure a safe environment and proper documentation.
Conclusion
So, you think skipping asbestos inspections is a great idea? Imagine living in a house where every wall whispers, "Surprise! I'm toxic!" Ignoring these inspections is like playing hide-and-seek with a ghost: thrilling until you realize it's haunting your health. By prioritizing inspections, you're not just dodging potential hazards; you're ensuring a safer environment for yourself and loved ones. So don't let your home become a hazardous amusement park—get those inspections done and breathe easier!