As a homeowner, you need to know that asbestos is a hazardous material often found in older buildings. Before any renovation, conduct a professional inspection to identify asbestos-containing materials (ACMs). Remediation must be handled by certified professionals who follow strict regulations set by the EPA and OSHA. They'll prepare the site, using proper protective gear and containment techniques to prevent fiber release. Waste disposal must comply with local hazardous material laws. Understanding these key facts is crucial for safeguarding your property and health, and there's more to ponder regarding compliance and safety measures.
Understanding Asbestos
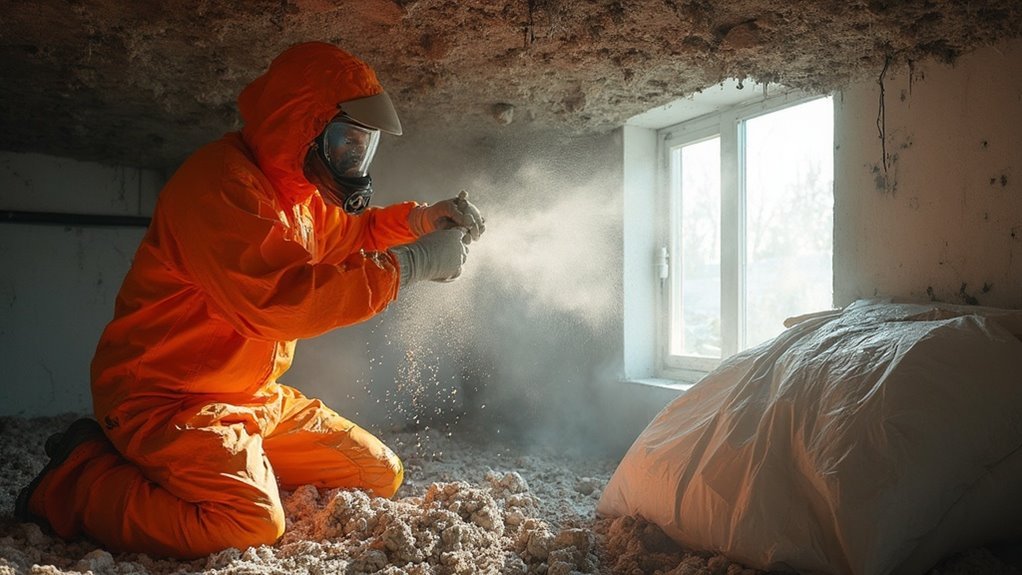
Understanding asbestos begins with recognizing its various types and their distinct properties. There are six recognized asbestos types: amosite, chrysotile, tremolite, actinolite, anthophyllite, and crocidolite. Each type has unique characteristics that influence its applications and associated health risks. For instance, amosite, crocidolite, and the other amphibole types are known for their straight fibers, while chrysotile, part of the serpentine class, features curved, tubular fibers.
Asbestos fibers are chemically inert and resist harsh conditions, which has led to their historical use in various products. Nevertheless, this durability comes at a cost. Significant exposure to any asbestos type increases your risk of severe health issues, including lung cancer, mesothelioma, and asbestosis. Long-term exposure to asbestos significantly raises the likelihood of developing these conditions, which may not manifest until 20 to 50 years post-exposure, making early detection challenging. Symptoms like coughing and shortness of breath are often overlooked, yet they signal potential health risks. Asbestos testing is crucial for identifying and managing these risks effectively.
Importance of Inspection
Identifying asbestos risks through thorough inspection is vital for ensuring safety compliance and preventing costly damage to your property. By engaging certified inspectors, you can accurately assess potential hazards and adhere to legal requirements. This proactive approach not just protects health but likewise mitigates unexpected expenses during renovation or demolition projects. Additionally, regular monitoring of Asbestos Containing Materials (ACMs) is essential to prevent health risks associated with prolonged exposure.
Identifying Asbestos Risks
Professional inspection is fundamental for effectively identifying asbestos risks in any environment, as even minimal exposure can have serious health implications. Relying solely on visual inspection isn't enough; professional asbestos testing is imperative to confirm the presence of harmful materials. Asbestos exposure can lead to severe long-term health consequences, including mesothelioma, asbestosis, and lung cancer, making early detection crucial.
Certain groups, such as construction and DIY renovation workers, face heightened risks. Unfortunately, exposure symptoms often take decades to manifest, underscoring the importance of proactive measures. Immediate symptoms may not be evident, so understanding the potential risks is significant. If you suspect asbestos in your home, an extensive inspection is necessary.
The inspection process involves evaluating suspected areas, inventorying potential asbestos-containing materials, and collecting bulk samples for laboratory analysis. Techniques like phase contrast polarized light microscopy (PLM) and scanning electron microscopy (SEM) can accurately identify asbestos fibers, ensuring you receive precise results. By addressing asbestos risks through professional inspection, you protect your health and that of others, preventing exposure-related diseases before they develop.
Ensuring Safety Compliance
Asbestos inspection is a vital step in guaranteeing safety compliance in any renovation or demolition project. You must adhere to safety regulations established by the EPA, OSHA, and more stringent local and state laws. Certified asbestos inspectors should conduct these inspections to assure accuracy and safety. The process typically involves visual examinations and sampling of suspected materials for laboratory analysis to confirm the presence of asbestos.
After the inspection, you'll receive a detailed written report that outlines findings and recommendations for abatement, if necessary. This documentation is fundamental for compliance audits and guarantees that all procedures align with federal, state, and local regulations.
It's important to understand that thorough inspections not only protect the health of workers and occupants but also mitigate legal risks. By following these guidelines, you can confidently move forward with your project while making sure that your actions are compliant with all safety regulations. Proper inspection serves as the foundation for developing a detailed abatement plan, laying the groundwork for safe and effective asbestos management. Always remember that non-compliance can lead to significant legal and health consequences, making inspections an irreplaceable part of your project.
Preventing Costly Damage
In any renovation or demolition project, early detection of asbestos is vital to preventing costly damage. Identifying asbestos before it deteriorates can save you from extensive contamination and expensive remediation down the line. By conducting thorough inspections, you'll not just adhere to regulations but likewise protect your financial planning with accurate cost estimates for any necessary abatement.
Early Detection Benefits | Consequences of Neglect | Proactive Testing Advantages |
---|---|---|
Saves future financial troubles | Higher risk of damage | Guarantees compliance with laws |
Prevents widespread contamination | Legal fines and actions | Maintains property value |
Guides effective abatement plans | Unforeseen financial burdens | Informs safe renovation planning |
Neglecting to test for asbestos can lead to hazardous situations, including the release of harmful fibers. This could not just jeopardize your health but likewise lead to a significant depreciation in property value. Regular inspections are a vital step in maintaining safety and guaranteeing that your renovation projects remain on budget while avoiding hidden costs. Don't overlook this significant aspect of home management.
Abatement Planning Steps
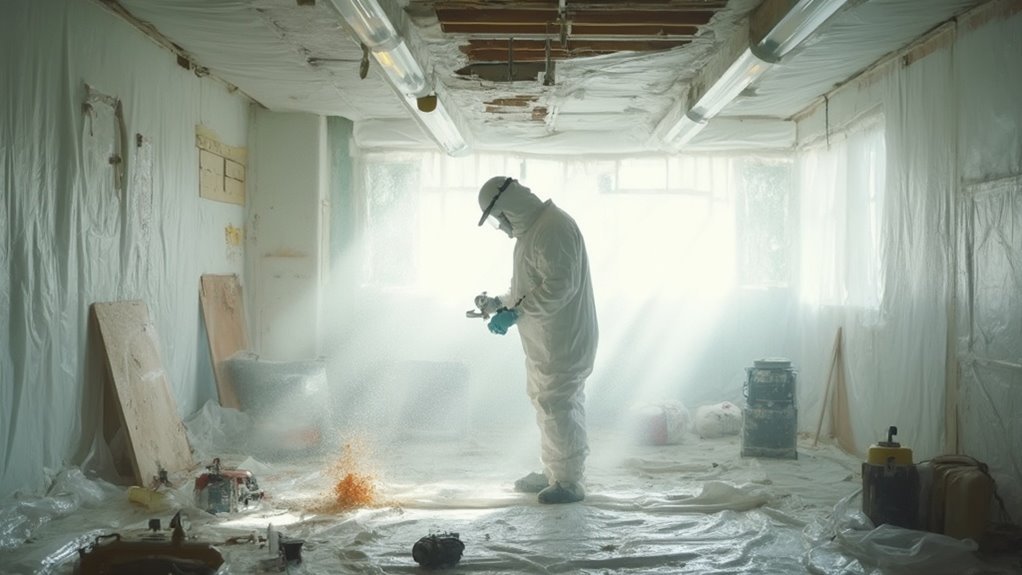
A successful abatement project begins with careful planning and assessment. First, identify all asbestos-containing materials (ACMs) through thorough inspection and testing. This initial step will help you determine the scope of the project, including the size and complexity of the removal process. Recognizing the need for certified professionals is essential; they'll guarantee compliance with safety regulations and effective handling of ACMs.
Next, develop a detailed work plan that outlines the abatement timeline and responsibilities for each stage of the project. This will aid in effective project budgeting, allowing you to allocate resources appropriately and avoid unexpected costs.
Pre-removal preparations are critical. Seal off the work area with plastic sheeting and turn off HVAC systems to prevent asbestos fibers from spreading. Verify all personal belongings are removed, and establish clear communication systems for any arising issues.
Lastly, prioritize safety by utilizing proper personal protective equipment and ventilation systems. Document every step, from inspections to waste disposal, confirming adherence to EPA and OSHA regulations. Following these planning steps will set the foundation for a safe and efficient asbestos abatement process.
Containment Techniques
Proper containment techniques are vital for maintaining safety during asbestos abatement. You'll need to use clear poly sheeting as your primary containment material to construct a non-porous barrier around the contaminated area. Secure this sheeting using Raptor Grip Poly Tape to create an airtight seal. It's imperative to seal all vents connected to the building's ventilation system and turn off the ventilation in the work area to prevent any asbestos fibers from escaping.
Implement negative air pressure machines equipped with HEPA filters within the containment zone. These devices help control air quality by filtering out airborne asbestos particles, guaranteeing they don't spread to other parts of your property. Your containment area should be designed to completely isolate the contaminated space, utilizing air scrubbing techniques to maintain safety for those outside the zone.
For smaller amounts of asbestos-containing material (ACM) or areas with limited access, consider using enclosure techniques. This involves constructing a permanent barrier with studs and polyethylene, sealing all edges with duct tape for maximum security. By following these containment methods, you can effectively minimize the risk of asbestos exposure during the abatement process.
Removal Processes
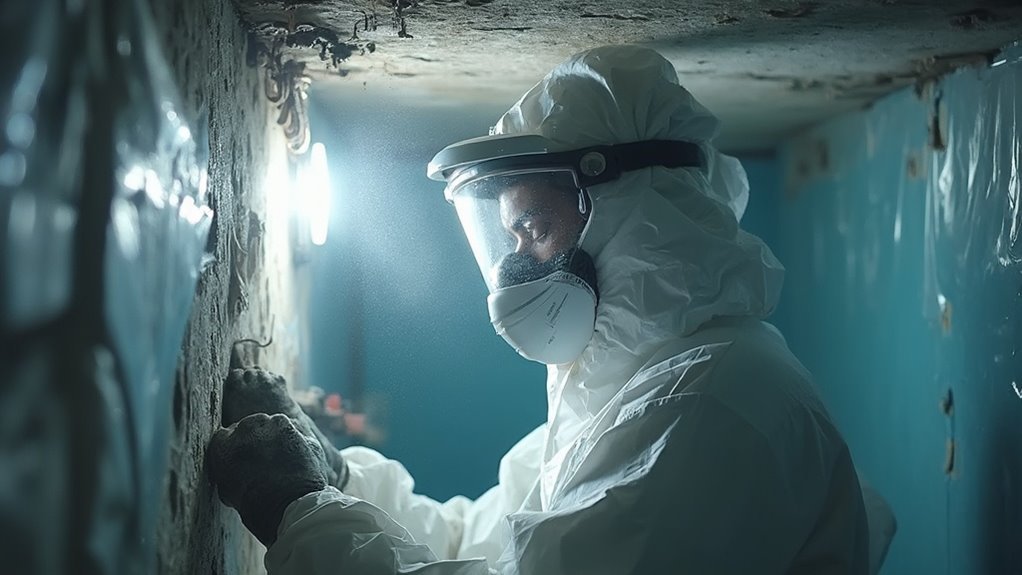
When you're ready to begin the asbestos removal process, using safe removal techniques is vital to minimize health risks. You'll need to wear appropriate protective gear to shield yourself from exposure while handling asbestos materials. Furthermore, understanding proper waste disposal methods guarantees that you comply with regulations and prevent environmental contamination.
Safe Removal Techniques
Asbestos removal requires meticulous planning and execution to guarantee safety and compliance with regulations. You must understand the crucial removal techniques and adhere to safety protocols during the process.
Here's a summary of the safe removal techniques you should be aware of:
Step | Description | Purpose |
---|---|---|
Inspection and Testing | Licensed inspectors identify and analyze asbestos. | Verify presence of asbestos before removal. |
Sealing Off Work Areas | Use plastic sheeting and negative air pressure. | Prevent fiber spread and isolate the area. |
Wet Removal Process | Wet materials to minimize dust during removal. | Reduce the release of asbestos fibers. |
Leak-tight Containers | Seal asbestos materials in secure containers. | Guarantee safe transport and disposal. |
Air Quality Testing | Conduct tests post-removal to check safety levels. | Verify area is safe for re-entry. |
Protective Gear Requirements
During the asbestos removal process, wearing the right protective gear is critical to confirm your safety and compliance with regulations. Begin with respiratory protection; you'll need a half-face filter respirator equipped with class P1 or P2 filter cartridges, adhering to Australian Standard AS1716. Ascertain a proper fit through a fit check, and remember, if you're male, being clean-shaven is crucial for an airtight seal.
For body protection, opt for Type 5, Category 3 disposable coveralls, complete with hoods and elasticised cuffs. Wear disposable gloves, guaranteeing they're tucked under your coveralls. Choose gumboots without laces for easy cleaning, and secure disposable shoe covers over your footwear.
Eye protection is just as significant; use protective eyewear to shield against dust exposure. After completing the removal, conduct thorough decontamination of all gear, tools, and your person. Remember, no PPE should be reused; all items must be treated as asbestos waste post-job. Following these safety standards will help you minimize exposure risks and confirm a safer environment during the abatement process.
Waste Disposal Methods
Once you've completed the asbestos removal process, proper waste disposal methods are vital to guarantee safety and compliance with regulations. Effective waste management guarantees that asbestos-containing materials (ACMs) are handled appropriately to prevent exposure.
Start by placing the asbestos waste in sealed, air-tight containers. This prevents any potential leakage during transport. For small amounts, double-bagging the materials and wetting them can further minimize fiber release. It's imperative that these waste containers are clearly labeled to inform handlers of the hazardous contents.
Next, transport the waste to certified landfills that are specifically licensed to accept asbestos. These facilities follow strict regulations governing disposal methods to safeguard public health and the environment. Alternatively, non-friable ACMs can be taken to solid waste transfer facilities.
In some cases, recycling options exist. Certain ACMs can undergo high-heat treatment processes to convert them into non-toxic ceramic fibers, offering a more sustainable disposal method.
Cleaning Protocols
Effective cleaning protocols are essential in minimizing the risk of asbestos fiber exposure during abatement activities. Start your process by sealing HVAC units and vents to prevent airborne fibers. Use plastic sheeting to contain the work area and perform wet wiping methods to minimize dust disturbance. Equip yourself with HEPA-filter vacuums for pre-cleaning, guaranteeing that you're not spreading asbestos fibers.
When it comes to wetting asbestos materials, thoroughly spray surfaces with a low-pressure solution, maintaining wet conditions throughout the removal process. Avoid high-pressure jets, as they can increase fiber release. Use non-powered hand tools to limit dust generation and carefully lower sheets of asbestos to minimize damage.
Post-removal cleanup is similarly important. Utilize wet cleanup tools and HEPA vacuums to thoroughly clean the area, and double-bag any asbestos debris in leak-tight containers. Decontaminate your equipment to confirm no fibers remain. Finally, shower and wash hands immediately after the work to remove any potential contaminants. Following these cleaning methods and adhering to safety protocols will greatly reduce your risk during asbestos abatement.
Disposal Regulations
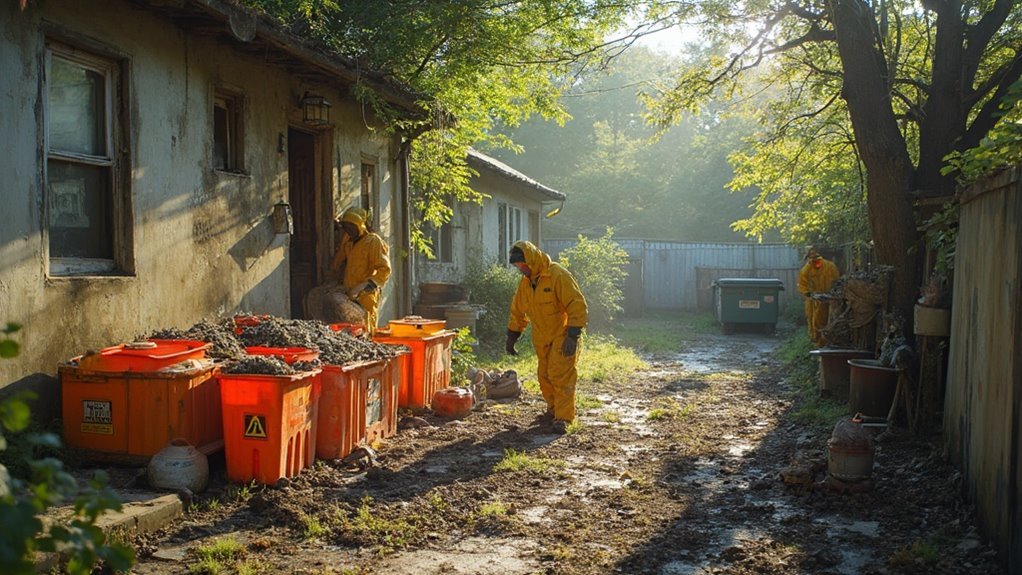
After completing the cleaning protocols, proper disposal of asbestos waste becomes a vital next step. Adhering to disposal regulations not only guarantees safety but likewise compliance with current regulatory updates. Here are key points to remember:
- All asbestos waste must be sealed in leak-tight containers and labeled appropriately.
- Transport vehicles need clear asbestos labels and should be operated by trained personnel.
- Final disposal requires licensed landfill facilities equipped for hazardous waste.
You must seal asbestos-containing materials in double-bagged containers, using an inner red bag and an outer clear bag. These containers should be locked and covered when not in use. When transporting, confirm the waste is handled securely to prevent any fiber release.
Asbestos waste must be taken directly to licensed disposal sites with dedicated landfill cells, preventing interaction with other waste types. Compliance with the Asbestos NESHAP involves notifying local authorities before any renovation or demolition work, guaranteeing proper inspection and adherence to work practice standards. Following these disposal methods is essential for maintaining safety and regulatory compliance throughout the abatement process.
Health and Safety Measures
When dealing with asbestos abatement, prioritizing health and safety measures is fundamental to protect workers and occupants. Compliance with health regulations guarantees that the abatement process is effective and safe. Here are key measures to implement:
Safety Measure | Description |
---|---|
Inspection and Assessment | Identify all asbestos-containing materials (ACMs) before work. |
Protective Gear | Enforce wearing full protective equipment like suits and gloves. |
Air Filtration | Utilize HEPA filter vacuums to capture asbestos fibers. |
Training Programs | Provide education on hazards and safety protocols for workers. |
Negative Air Pressure | Maintain negative pressure in work areas to prevent fiber escape. |
Regular inspections of properties for ACM wear and tear are significant. Avoid disturbing undamaged ACMs, and always consult professionals for renovation planning. Implementing rigorous training programs for workers on asbestos hazards and emergency procedures is critical. This guarantees they understand the importance of safety measures and personal protective equipment (PPE). By adhering to these health and safety measures, you minimize risks effectively during asbestos abatement activities.
Frequently Asked Questions
How Can I Identify Asbestos in My Home?
Imagine uncovering a hidden danger. You can identify asbestos in your home by using visual identification tips, like checking for fibrous materials. For certainty, consider professional asbestos testing methods to confirm presence and guarantee safety.
What Should I Do if I Suspect Asbestos?
If you suspect asbestos, schedule a professional inspection immediately. They'll conduct asbestos testing to confirm its presence safely. Avoid disturbing any materials yourself, as this could release harmful fibers into your home's air.
How Long Does the Abatement Process Typically Take?
The abatement duration can feel like an eternity, but typically, small projects take days, while larger ones may stretch for weeks. Always factor in project timeline complexities, accessibility, and safety measures for accurate estimates.
Can I Stay in My Home During Abatement?
During the abatement process, you should consider health concerns. If high-risk materials are involved or work occurs in occupied areas, temporary relocation is often necessary to guarantee your safety and minimize exposure to asbestos fibers.
What Are the Signs of Improper Asbestos Removal?
Improper asbestos removal can expose you to hazardous fibers. Signs include unqualified workers, inadequate safety measures, and improper disposal methods. Always guarantee removal safety by verifying certifications and adhering to regulatory standards for protection.