If your property was built before 1975, there's a significant chance it contains asbestos, as approximately one in three homes from that era does. Asbestos inspections are essential for identifying hazardous materials and guaranteeing compliance with federal and state regulations. During an inspection, professionals assess for asbestos-containing materials (ACMs) and evaluate their condition. They perform visual checks and bulk sampling for lab analysis. Regular inspections and proper management can mitigate health risks associated with exposure, including lung cancer and asbestosis. You'll want to understand more about the inspection process and ongoing management strategies to make certain your property remains safe and compliant.
Understanding Asbestos Inspections
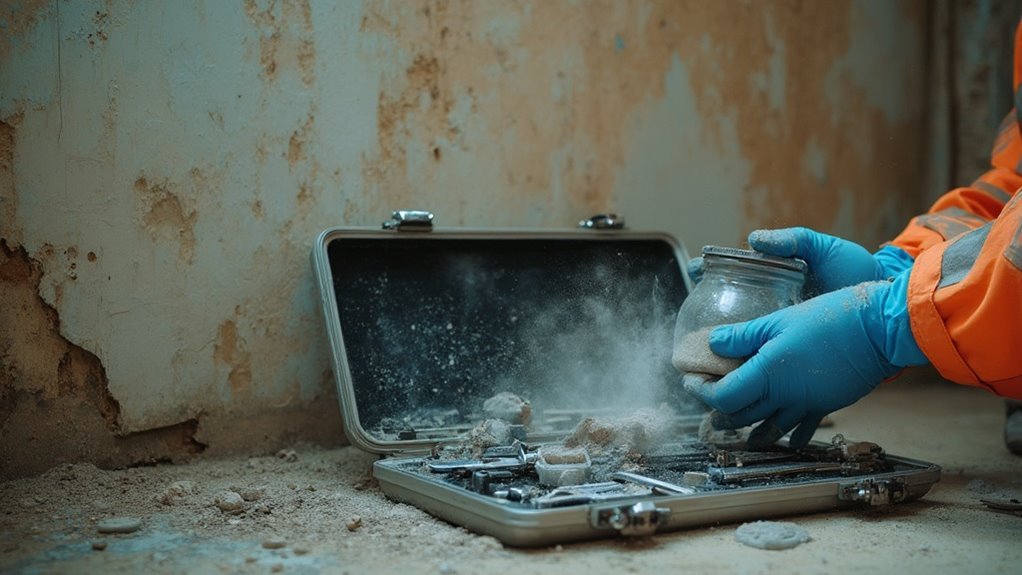
Asbestos inspections are crucial for identifying and managing hazardous materials in buildings. You might hear various asbestos myths that downplay the importance of these inspections, but understanding the process is fundamental for your safety. Initially, an assessment involves reviewing historical data and conducting interviews to identify potential asbestos-containing materials. Accessible areas are inspected to form a detailed inspection plan, documenting suspected materials for further examination.
During the physical inspection, a thorough visual examination is necessary to spot any damage or signs of deterioration. Sampling of suspected materials confirms the presence of asbestos and helps assess the associated risks. The collected samples are then sent to accredited laboratories for analysis, determining the type and concentration of asbestos present. Asbestos exposure is linked to lethal diseases, making these inspections even more critical. Additionally, properties built before 2000 are particularly at risk for asbestos due to the widespread use of asbestos in construction materials during that time.
Inspection costs can vary, but they're a necessary investment in protecting your health and your property. The final report provides a detailed overview of the property and includes recommendations for managing any identified asbestos materials. Whether it's repair, encapsulation, or removal, knowing the facts about asbestos inspections empowers you to make knowledgeable choices regarding your property's safety.
When Inspections Are Necessary
Identifying when inspections are necessary is vital for maintaining safety in properties that may contain asbestos. You should always schedule an inspection before renovations or demolitions, as federal, state, and local regulations mandate this to identify any asbestos-containing materials (ACMs). If you're buying or selling a property built before the 1980s or 2004, an inspection is important to guarantee safety and uphold due diligence.
Moreover, if your building shows signs of wear or has suffered damage—such as from natural disasters—you must arrange for an inspection. Asbestos management plans likewise require inspections, particularly for non-domestic properties constructed before 2000. Additionally, the presence of asbestos in homes can significantly affect property value, making inspections crucial for informed decision-making.
To maintain asbestos awareness, remember that existing plans require annual updates through reinspections, especially for buildings with known ACMs, unless they are deemed low risk with adequate controls.
Conducting an Asbestos Inspection
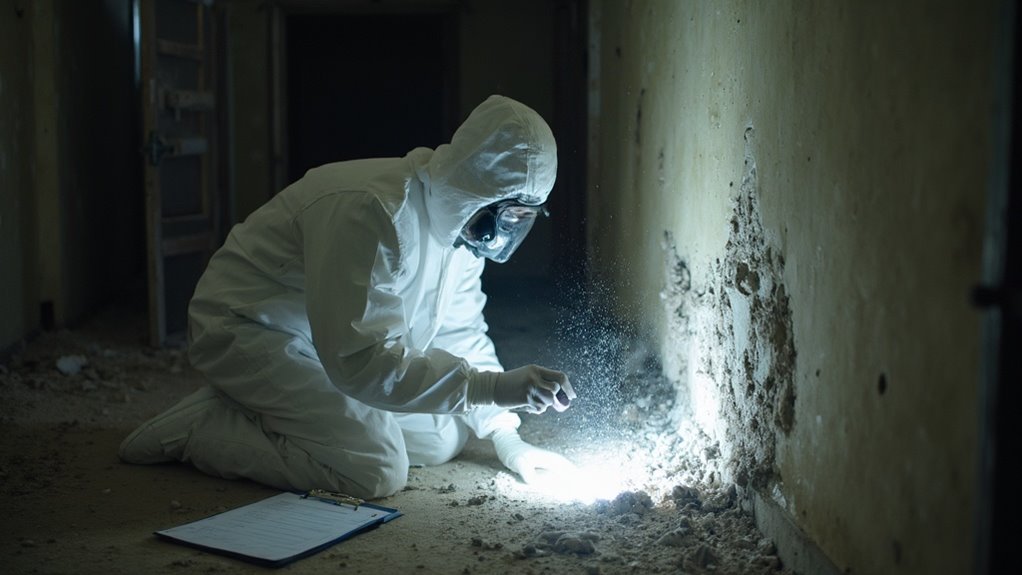
When conducting an asbestos inspection, you start with an extensive historical review and initial assessment to identify potential asbestos-containing materials. This process includes a detailed physical inspection and sampling to confirm the presence and condition of asbestos. Finally, you'll compile a thorough report that categorizes your findings, guiding future management actions.
Inspection Process Overview
Conducting an asbestos inspection involves thorough preparation and systematic assessment to guarantee safety and compliance. To achieve accurate results, you should follow these vital steps:
- Pre-Inspection Preparation: Begin with a historical review and interviews to identify potential asbestos-containing materials. Perform an accessible area inspection and create a survey plan outlining the scope and sampling strategies.
- Inspection and Sampling: Conduct a detailed physical examination, looking for any signs of damage or degradation. Use appropriate inspection technologies and tools, such as Stanley knives and core borers, to collect samples from various materials. Verify samples are sealed in airtight bags for safe transport.
- Post-Inspection Activities: Based on findings, develop a management plan that may include repairs, encapsulation, or removal of asbestos materials. Provide a written statement verifying compliance with AHERA standards.
Debunking common asbestos myths is vital during this process, as misinformation can lead to inadequate safety measures. By adhering to these steps, you can effectively confirm that your property is inspected accurately and responsibly, minimizing risks associated with asbestos exposure.
Key Assessment Techniques
Utilizing a variety of assessment techniques is vital for effectively conducting an asbestos inspection. Start with a thorough visual inspection of building spaces to identify potential asbestos-containing materials (ACMs). Focus on asbestos identification by examining materials based on appearance and historical context. Following this, evaluate the condition of these materials through damage evaluation to determine any degradation that could release asbestos fibers.
When sampling, extract bulk samples from suspected ACMs, guaranteeing you collect enough for accurate laboratory analysis. Store these samples securely and handle them in controlled environments to prevent fiber release. For laboratory analysis, use methods like Polarized Light Microscopy (PLM) and Transmission Electron Microscopy (TEM) for precise identification of asbestos fibers.
Documenting your findings is vital. Classify materials as homogeneous or non-homogeneous to inform sampling strategies. Once you complete your assessment, provide a detailed written report that includes your findings, recommendations for managing or removing ACMs, and maintain records for future reference. This all-encompassing approach guarantees a thorough evaluation and helps safeguard against potential asbestos risks in your property.
What to Expect in an Inspection Report
In your inspection report, you'll find key components that outline the condition and location of any asbestos-containing materials (ACMs) identified. This information is essential for developing effective risk management strategies to guarantee safety and compliance with regulations. Understanding these elements will help you make knowledgeable choices regarding remediation and ongoing monitoring.
Key Report Components
An asbestos inspection report is an essential document that provides important information about the presence and condition of asbestos-containing materials (ACMs) within a property. Understanding its key components guarantees you grasp the report's accuracy and the significance of inspection frequency.
Here's what you can expect in an inspection report:
- Summary and Methodology: The report begins with a summary detailing the site, the type of survey (Management or Renovation/Demolition), and the methodology used for identifying ACMs.
- Findings and Asbestos Register: Main findings include a thorough list of identified ACMs, their locations, types, and conditions. This section is significant for ongoing management.
- Visual Evidence and Compliance: Expect photographs and site plans that visually document ACMs, along with laboratory results confirming analysis. The report should likewise include the inspector's credentials and compliance with relevant standards.
Risk Management Strategies
Regularly implementing effective risk management strategies is crucial for addressing potential hazards associated with asbestos-containing materials (ACMs). When you receive an inspection report, you can expect a thorough risk assessment that identifies ACMs and evaluates their condition. The report will outline necessary control measures tailored to the identified risks.
Here's a summary of what you might find in your inspection report:
Survey Type | Purpose | Control Measures |
---|---|---|
Pre-Purchase Survey | Identify ACMs before purchase | Risk assessment, encapsulation |
Management Survey | Monitor ACMs in operational buildings | Routine assessments, enclosure |
Refurbishment Survey | Identify ACMs before renovations | Removal, strict procedures |
Demolition Survey | Assess ACMs that may be disturbed | Thorough risk assessment |
Regulatory Compliance | Guarantee adherence to OSHA and EPA | Documentation, training programs |
The inspection report will serve as a foundational tool for managing ACMs effectively. By understanding the findings and implementing the recommended control measures, you can greatly reduce risks associated with asbestos exposure. Regular monitoring and maintenance are crucial for ongoing compliance and safety.
Importance of Asbestos Inspections
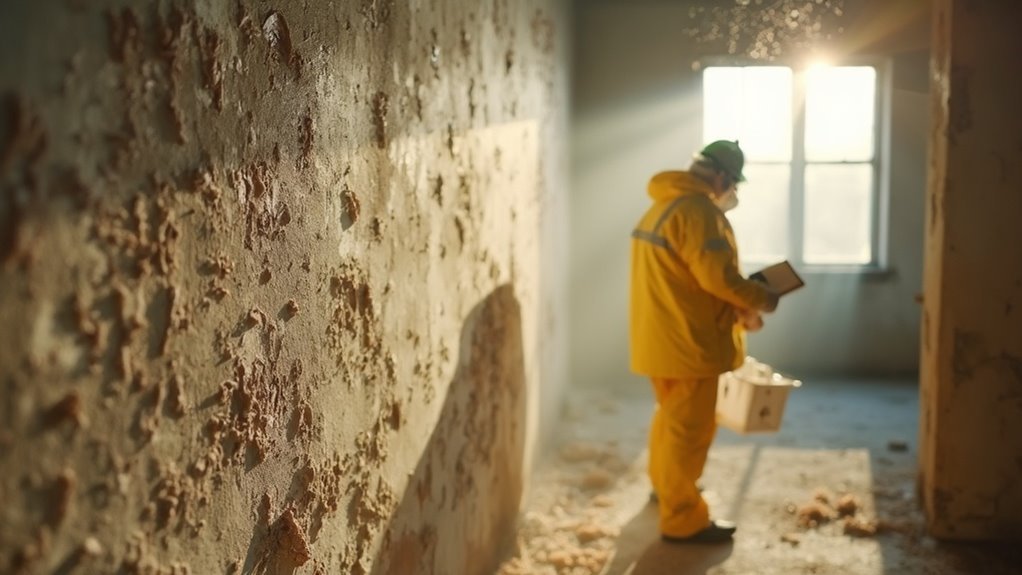
Asbestos inspections play a crucial role in maintaining safety and compliance in both residential and commercial properties. Understanding their importance can help you debunk asbestos myths and make knowledgeable choices, especially regarding inspection costs. Here are three key reasons why these inspections are critical:
- Regulatory Compliance: Asbestos inspections are mandated by federal, state, and local regulations. Ensuring compliance protects you from potential legal ramifications.
- Risk Management: Conducting an inspection before any renovation or demolition helps identify asbestos-containing materials (ACMs). This proactive approach mitigates risks associated with disturbing these materials.
- Cost Efficiency: Unexpected costs and delays can arise from not performing an inspection. By identifying ACMs early, you can plan for necessary abatement actions, ultimately saving you money.
Health Risks of Asbestos Exposure
Understanding the health risks associated with asbestos exposure is critical for anyone involved in properties where asbestos may be present. The asbestos dangers are significant, particularly for individuals who have prolonged exposure. Asbestos exposure increases the risk of developing serious diseases, most importantly lung cancer and mesothelioma. Symptoms of lung cancer can manifest as persistent cough, respiratory complications, or coughing up blood, often appearing decades after initial exposure.
Asbestosis, characterized by a slow build-up of scar-like tissue in the lungs, can impair lung function and lead to severe health issues. It presents with symptoms such as a dry cough and chest tightness. Furthermore, individuals who smoke and have been exposed to asbestos face a dramatically heightened risk of lung cancer.
The latency period for asbestos-related diseases can range from 20 to 50 years, making early detection challenging. Regular medical evaluations, including chest X-rays and breathing tests, are fundamental for identifying early signs. Awareness of these risks is important, especially for those in high-exposure professions like construction or shipbuilding, as it directly impacts your health and safety.
Steps After an Inspection
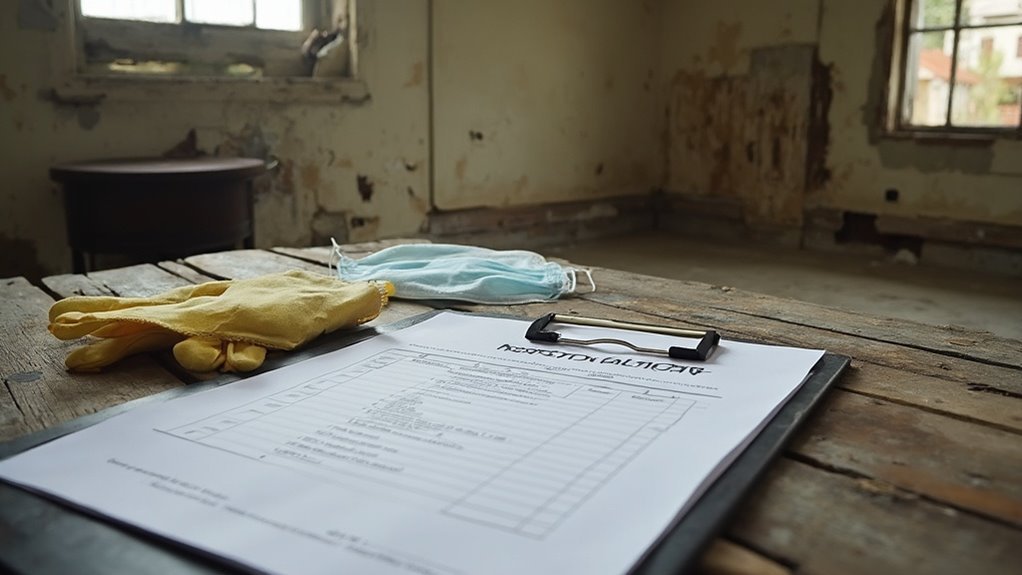
Following an asbestos inspection, it's fundamental to take immediate and systematic steps to guarantee safety and compliance with health regulations. Your next actions will hinge on the results of the asbestos testing and the necessary removal techniques employed.
- Cleaning and Decontamination: Use HEPA vacuum cleaners to eliminate residual asbestos fibers. Wet surfaces to prevent further fiber release and seal contaminated materials in labeled heavy-duty polythene bags. Dispose of all plastic sheeting used during removal as hazardous waste.
- Air Quality Testing: Conduct air quality tests to confirm that asbestos levels are below safe limits. Engage licensed professionals for these tests and obtain clearance before reoccupying the area. Regular inspections are vital for maintaining ongoing safety.
- Proper Waste Disposal: Transport asbestos waste to licensed disposal facilities, adhering strictly to local regulations. Use leak-tight containers for all materials and clearly mark them to indicate their contents, guaranteeing the safety of workers and the public.
Legal and Regulatory Compliance
Compliance with legal and regulatory requirements for asbestos inspections is vital for ensuring safety during renovation or demolition activities. You have legal obligations to conduct asbestos surveys before any work begins, regardless of your property's age. These surveys must be performed by certified asbestos consultants (CACs) in accordance with Rule 1403 and 40 CFR Part 763.
Your asbestos survey report should include detailed findings such as the scope of the survey, facility description, date of inspection, and attachments like sample chain of custody and laboratory analysis results. Failing to comply with these regulations can expose you to significant legal risks, including fines and liability for health impacts.
Both state and federal regulations mandate these compliance requirements, ensuring that all potential asbestos-containing materials (ACMs) are identified and managed appropriately. For instance, the San Diego Air Pollution Control District Rule 1206 requires surveys even in emergency situations, reaffirming that compliance is not optional.
Ultimately, regular updates to your asbestos register and adherence to these legal standards are vital for protecting both your property and the health of anyone who might be affected.
Educating About Asbestos Safety
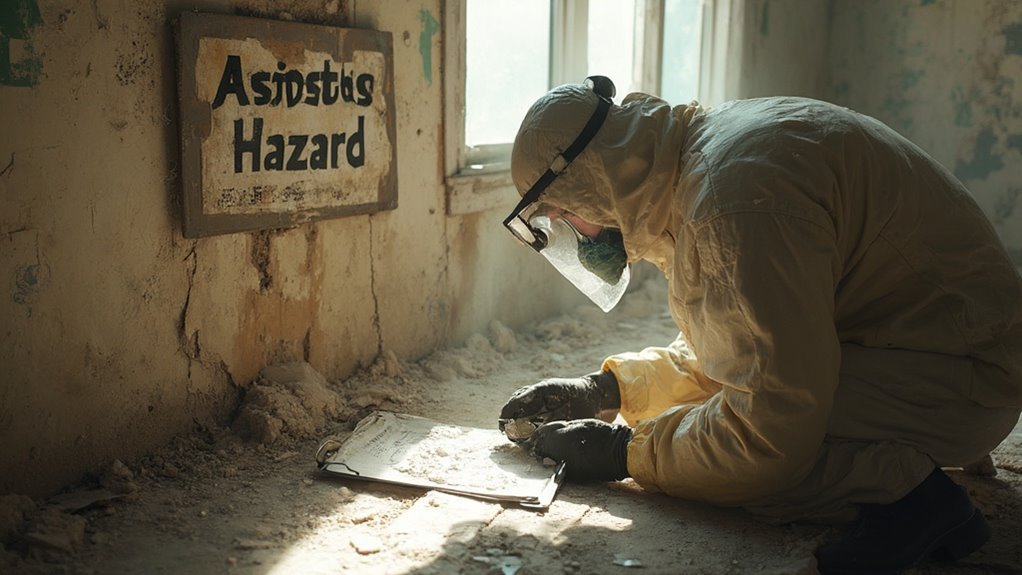
Asbestos safety education is fundamental for anyone working in environments where asbestos may be present. Understanding the facts and dispelling common asbestos myths can greatly reduce health risks. Proper training equips you with important knowledge about safety protocols and best practices.
Here are three key components of asbestos safety education:
- Understanding Asbestos Risks: Familiarize yourself with the health effects related to asbestos exposure, like mesothelioma and asbestosis.
- Identification of Asbestos-Containing Materials (ACM): Learn how to recognize materials that may harbor asbestos, making sure you can identify potential hazards in buildings.
- Safe Handling Practices: Master the procedures for safely working around or handling ACM, which is critical to maintaining a safe work environment.
Regular training is not just a regulatory requirement; it's important for your safety and that of your colleagues. Remember, compliance with OSHA and EPA regulations guarantees that you're not only informed but prepared to respond appropriately in emergencies. By investing in asbestos safety education, you're taking a considerable step toward protecting yourself and others from the risks associated with asbestos exposure.
Frequently Asked Questions
How Much Does an Asbestos Inspection Typically Cost?
Asbestos testing costs typically range from $225 to $808, depending on factors like property size and inspection service rates. Extensive inspections may reach $1,500, reflecting the complexity and thoroughness of testing required.
How Long Does an Asbestos Inspection Usually Take?
Asbestos assessment activities vary; the inspection duration hinges on the building's size and complexity. Typically, the asbestos testing process takes a few hours to several days, ensuring thorough evaluation and accurate results for your property.
Can I Conduct an Asbestos Inspection Myself?
You shouldn't conduct asbestos testing yourself, as it poses health risks. Professional inspectors use reliable methods and expertise to guarantee safe, accurate results, minimizing exposure and adhering to legal regulations for your safety.
What Should I Do if Asbestos Is Found?
If you find asbestos, prioritize safety. Engage a licensed professional for asbestos abatement. They'll assess health risks, develop a removal plan, and guarantee compliance with regulations to minimize exposure and protect your well-being.
How Often Should I Schedule Asbestos Inspections?
If you're managing an older school, you should schedule asbestos inspections every six months because of asbestos regulations. This inspection frequency guarantees safety and compliance while addressing the potential risks of deteriorating asbestos-containing materials.